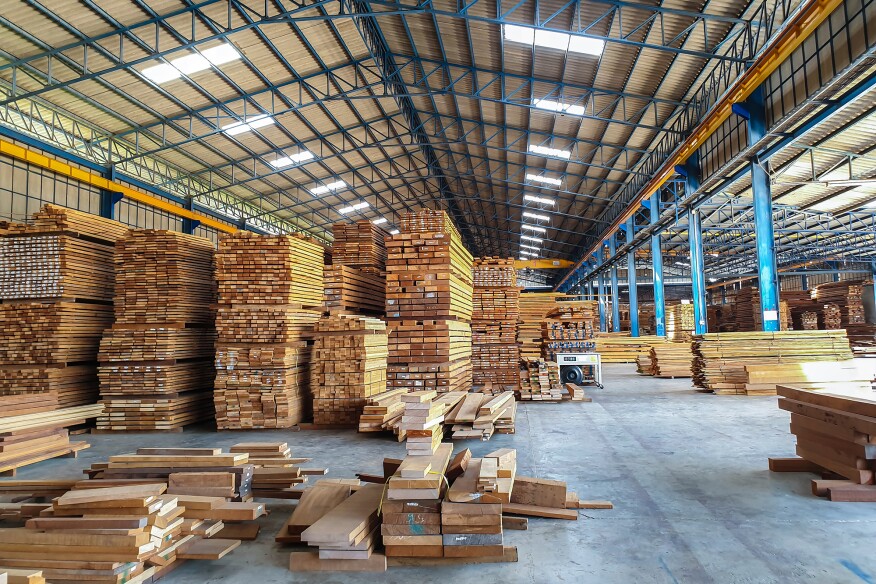
As COVID-19 began to spread throughout the world’s urban centers in 2020, the pandemic revealed vulnerabilities not only in public health but also in material supply chains. In the U.S., the super disruption of resource flows wreaked particular havoc on the lumber industry, which experienced its most significant price increase since the housing boom after World War II. “The lumber industry’s weaknesses revealed the need to focus on viability within a dynamic and responsive model that integrates and operationalizes adaption at different stages of a crisis,” wrote economist Alexander Franco in The Pandemic Effect.
Given the inevitability of ongoing supply chain disruptions caused by natural disasters, global resource competition, and future pandemics, construction industry leaders aspire to make material management and procurement processes much more reliable. It should be no surprise that artificial intelligence is quickly revealing its effectiveness in achieving this aim. A year into the pandemic, the global consulting firm McKinsey & Company published a report recommending the adoption of AI tools to enhance the adaptability of material resource flows. The article’s authors proposed the use of AI technologies in five dimensions of the product supply chain: planning, logistics and distribution, production, procurement, and marketing and sales. The report also advocated the deep integration of these traditionally isolated functions in large companies, using the analogy of a “central cross-functional brain."
A recent proliferation of AI-powered tools is beginning to fulfill this need. For example, Miami-based software company DigiBuild has developed AI-based services to address what it calls the construction industry’s “biggest pain points” of material supply chain and risk management. According to the start-up, typical building projects remain “80% over budget and 20 months behind schedule,” with 20% higher material costs and 50% longer lead times as a direct result of ongoing material supply chain management challenges. The 5-year-old minority- and woman-owned company offers two innovative AI platforms to combat these challenges: DigiEndeavor for construction project planning and management and DigiProcure for building material ordering and tracking. DigiBuild CEO Robert Salvador describes the new tools as “supersonic” compared with prior approaches, explaining to Fox Business that it is now possible “to talk to 100 suppliers in one minute versus maybe a handful in a couple hours."
Centralizing product tracking is also a primary goal for San Francisco–based Kojo, another AI-powered, woman-owned materials management firm founded around the same time as DigiBuild. According to ConstructionDive, Kojo addresses the fragmented nature of the construction process. On a typical project, the general contractor does not have a comprehensive understanding of the procured materials, as individual subcontractors typically purchase them. This lack of knowledge and decision-making control can lead to unwanted surprises, resulting in delays and cost overruns. Kojo’s management software assembles all procurement data to provide clear oversight of supply chains. According to company founder and CEO Maria Davidson, Kojo has been instrumental in reducing manual data entry by 75%, construction waste by 90%, and material costs by $22 million.
Newark, N.J.-based Algoscale Technologies outlines six fundamental ways that AI can enhance construction, ranging from the planning to the implementation phases of the material management process. Predictive analytics and demand forecasting scrutinize large quantities of data from many sources to deliver insights regarding potential procurement delays and inventory challenges. Supplier selection provides a qualitative assessment of suppliers based on their reliability, delivery speeds, and product quality. Route optimization and fleet management enable increased efficiency in transportation costs, including fuel consumption and carbon footprint reduction. Risk mitigation offers a holistic supply chain-monitoring function, alerting contractors early to potential budget- and timeline-related surprises. Algoscale documented a case study where a contractor utilized a centralized data repository supported by a suite of Software as a Service tools to enhance its bidding and procurement processes. The result included a 75% shorter bid-preparation time, lower acquisition costs, and increased project bidding capacity.
The dramatic growth of AI-powered supply chain management offerings suggests that the technology sector has become increasingly aware of what AEC professionals have long known: The construction industry—which accounts for some 13% of global GDP yet has only seen 1% annual growth—can use a productivity boost. Another McKinsey report explains that “the industry’s productivity has trailed that of other sectors for decades, and there is a $1.6 trillion opportunity to close the gap.” This $1.6 trillion value boost, accelerated by AI tools, could fulfill significant building needs in more resourceful ways.
Until now, implementing meaningful industry-wide improvements has been a challenge, but measurable changes now seem imminent. "Before companies like us, the construction industry was still early in its digital transformation—they were late to the party," Salvador explained to FOX Business. Now, however, "It's very much going all in on that, finally.”
The views and conclusions from this author are not necessarily those of ARCHITECT magazine or of The American Institute of Architects.
Read more: The latest from columnist Blaine Brownell, FAIA, includes looks at pre-20th-century construction's clues to tackling climate change, emerging carbon capture and storage technologies, and the blue economy.